"If
the Earth Had a Voice it Would be the Didgeridoo"
Technical
info |
Clear
bass and a sharp 'edge' are two attributes that Echo Tree's
didgeridoos are known for. One of the reasons for this is because
of the timber we use. This timber is extremely dense; denser
than Ironbark in fact, one of Australia's well known, hard native
timbers. Because of this we continue to predominantly use arid
grown 'Greybox' to craft or didgeridoos. The extreme density
of this timber largely contributes to the great 'edge' our instruments
produce. We of course do not exclude the use of other timber
types in our hancrafting process and are sure that our continuing
research will further expand the knowledge about this unique
instrument. |
|
|
|
Didgeridoo Collection
Echo Tree only make their didgeridoos from sound,
good quality Australian timbers that have been naturally hollowed
out by termites (sometimes incorrectly called white ants). These timbers
are personally selected by our craftsmen.
|
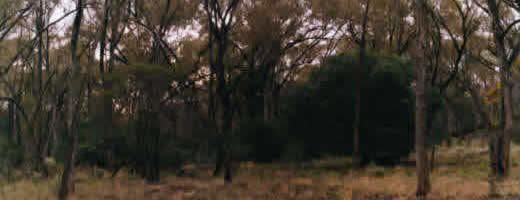 |
Echo Tree only make their didgeridoos from sound, good quality Australian
timbers that have been naturally hollowed out by termites (sometimes
incorrectly called white ants). These timbers are personally selected
by our craftsmen.
Once we have selected our didgeridoo, the next step is to clean the
termite waste from the inside of the hollow
tree.
|
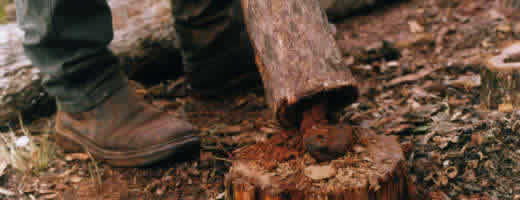 |
I
Back
to Top I
|
|
Didgeridoo
Seasoning
|
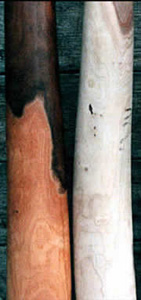 |
After
the hollow tree has been cleaned out we place it under controlled
conditions to season. With the bark still on, we leave our timber
to season for a minimum of one and a half years before it is ready
for the didgeridoo handcrafting process. |
Technical
info |
The
main reason that many didgeridoos crack and split after purchase
is that they are made from timber that is 'green' or unseasoned.
Green timber is very unstable and as it dries out in uncontrolled
conditions it will often split. Another reason many didgeridoos
fail a short time after purchase is because they are not properly
treated and sealed. A didgeridoo made from unseasoned, untreated
and unsealed timber can still legitimately be called 'genuine'
or 'authentic' but will not necessarily be of a high quality
standard. |
|
I
Back
to Top I
|
|
The
Handcrafting Process
|
The
handcrafting process is now ready to begin. Starting with a coarse
sand paper and working down to a very fine grade, the didgeridoo is
sanded back to reveal the beautiful native Australian wood grain that
lies beneath.
Once we have our instrument at this stage, the Echo Tree emblem is
etched into the timber. The emblem is located on the back of the didgeridoo
near the base. A serial number is also burnt into the wood, just beneath
the emblem. |
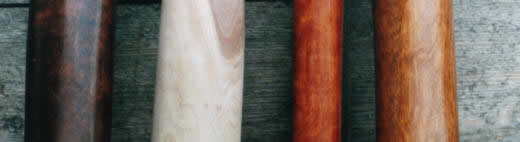 |
Technical
info |
We
choose not to use 'dowels' or wooden 'plugs' to seal imperfections
in our instruments. The rate of expansion of a dowel will always
be different to that of the side grain of a didgeridoo. This
will result in failure of the integrity of the instrument.
Echo Tree starts with premium raw materials and this is another
reason why our finished product is such high quality. |
|
I
Back
to Top I
|
|
Outside
Finish
Every
instrument we handcraft is sealed both inside and out. We seal the
inside to protect it from the moisture and humidity that results from
a player's breath. If the inside is not sealed, the constant hydration
and dehydration (wetting and drying) that will occur with use will
age and crack the instrument from the inside out. This can eventually
lead to air leaks and the need for costly repair.
The outside is sealed for similar reasons but with the added function
to enhance the beauty of the wood grain and/or Aboriginal artwork
it protects. |
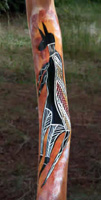 |
Technical
info |
The
outside is sealed to protect the instrument from humidity, temperature
changes, moisture, contaminants (e.g. from the skin), sunlight
and mild mechanical damage. Because we place a guarantee on
all our didgeridoos it is imperative to us that we are able
to present them to the buyer in perfect condition. |
|
I
Back
to Top I
|
|
Didgeridoo
Mouthpiece
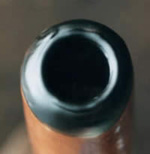
|
In
the final stages of our handcrafting process we hand mold a wax or
wooden mouthpiece, test it for 'playability' and then key the instrument.
The 'key' or note of the didgeridoo is important for its compatibility
when played with other musical instruments.
|
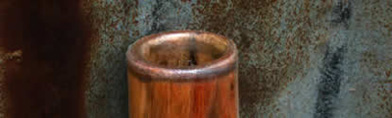 |
Because we offer both wood grain and painted instruments, we now select
which ones are to be sent to Aboriginal artists. |
I
Back
to Top I
|
|
Didgeridoo
Artwork
All
Aboriginal artwork that appears on an Echo Tree didgeridoo is a unique
hand painted indigenous creation. |
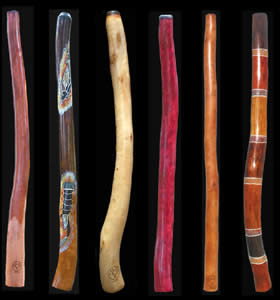 |
Once
artwork has been hand painted onto the instrument, a number of further
protective layers are applied to enhance and protect the artwork.
Finally we execute an extensive quality control check and test the
musical quality of each didgeridoo.
At this stage we also set our prices according to sound quality, artwork,
shape, aesthetics, etc.
With each finished didgeridoo we also include a 20-page information
booklet and mouthpiece protector. This completes the package and makes
the instrument ready for sale. |
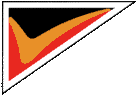
|
At
Echo Tree we are proud to place the NIAAA label on our didgeridoos.
The National Indigenous Arts Advocacy Association label is your assurance
of authenticity. |
Technical
info |
Another
consideration we have made is in regards to protection during
transit, particularly air travel. Unsealed or inadequately sealed
didgeridoos are susceptible to significant dehydration during
air travel because of the low humidity conditions that air cargo
is exposed to. By properly sealing our instruments we are able
to ensure that these conditions will not affect them or their
functionality in any way. |
|
I
Back
to Top I
|
|
We are
always interested in feedback about our didgeridoos and supporting products,
and welcome your contact. feedback@echotree.com.au
|